Category: Company News

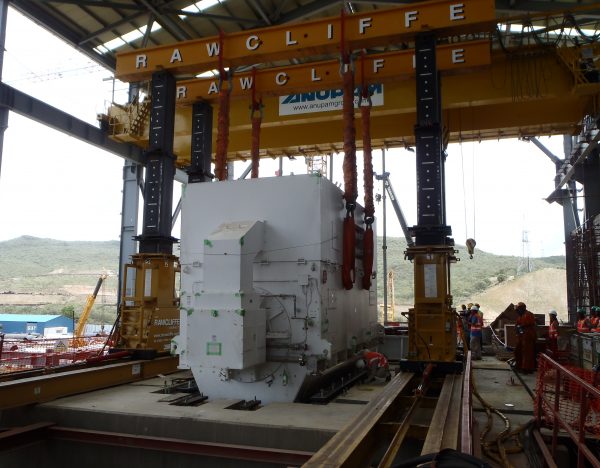
Venture Into Africa
In proving the company’s ability to operate internationally JB Rawcliffe & Sons Ltd have successfully completed a joint venture heavy lift project in Kenya, Africa with Coast Hauliers Ltd of Mombasa.
The project was 12 months in the planning in which a detailed method with associated storyboard had to be produced to prove the solution for the lifting of the generators 10m from ground level, travel of 11m over the plinth and then lowering of 1m to sole plates.
On being awarded the project JB Rawcliffe & Sons Ltd began with the design, calculations and manufacturing drawings of the required 9m high supports that would allow the lift system to travel off the edge of the plinth. One set of support steelwork was designed to allow the steelwork to be used for the four separate generator plinths. The approach was taken to design the support steelwork in modular form from steel sections allowing the support steelwork to be fabricated locally to site, allow the parts of the support to be transported economically and allow the support steelwork to be assembled in the least number of lifts.
JB Rawcliffe & Sons Ltd 500Ton capacity lift system comprising of 18m of runway track, 10m header beams, power packs, and all required lifting equipment was packed into three conventional shipping containers which allowed for the easy shipping of the system to Kenya.
On arrival in Mombasa, the equipment was unpacked from the containers and delivered to site. JB Rawcliffe & Sons Ltd supplied operators to supervise and assist with the build of the support steelwork ensuring its integrity and level due to poor ground makeup. With assistance from local labour the lift system was assembled on the plinth and Cost Hauliers Ltd transported the 141,000kg generators from Mombasa Port to site.
Due to the location of the plinths within the power station building and limited room on site Coast Hauliers Ltd jacked the generators from the delivery trailer, rotated them 90degrees and skidded them beneath the lift system.
The joint venture heavy lift project with Coast Hauliers Ltd was a complete success with all four generators lifted and positioned on their sole plates without incident and within client’s schedule.
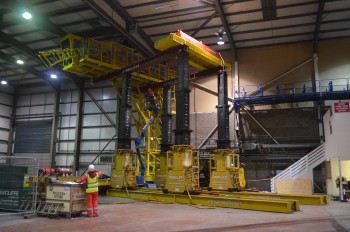
Innovative Lifting
Earlier this year saw JB Rawcliffe & Sons Ltd involved in a challenging lift not only in time but available room. The challenge was to lift a structure 2m within a building with only 2.5m of available headroom. Several ideas were discussed with the client until the ideal solution was decided on which created the least disruption and also by allowing other structures to remain in position accelerated the project. Using our hydraulic gantry lift system a counterbalance rig was engineered to produce a successful millimetre accurate lift.
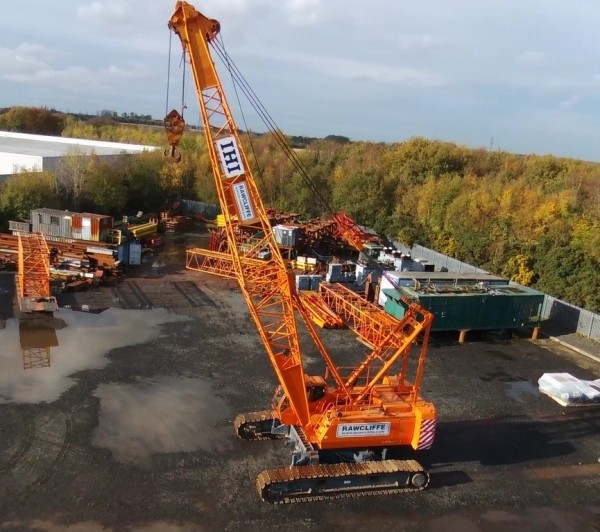
120,000kg Facility Upgrade
JB Rawcliffe & Sons Ltd is proud to announce the latest upgrade to the outside facility crane at Skelmersdale, Lancashire. The IHI CCH1200 replaces the Hitachi KH300/1 doubling the lift capacity available to 120,000kg at 5m radius. The primary use of the crane is for the placement of goods into outside storage with the crane available for the transhipment of goods from one vehicle to another. JB Rawcliffe & Sons Ltd 12 acre facility is fully secure with 24-hour security and monitored CCTV. Whether internally or externally, the company is able to off-load and place heavier pieces into storage using hydraulic gantry lift systems or jacking and skidding.
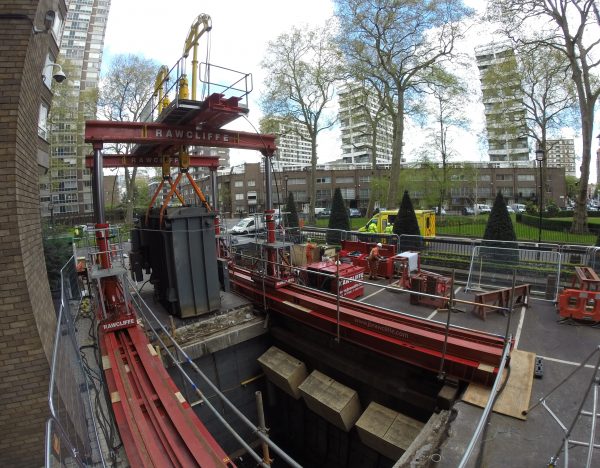
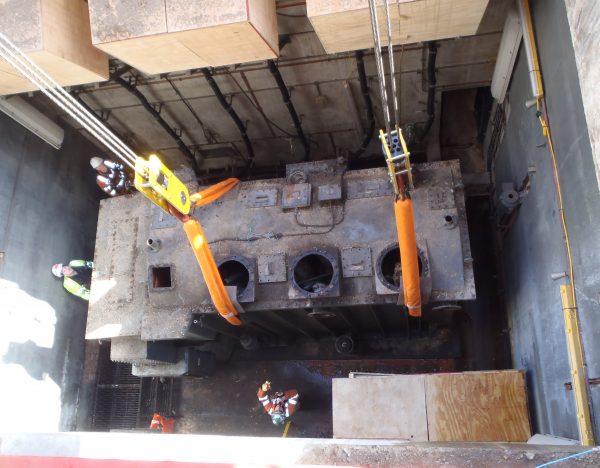
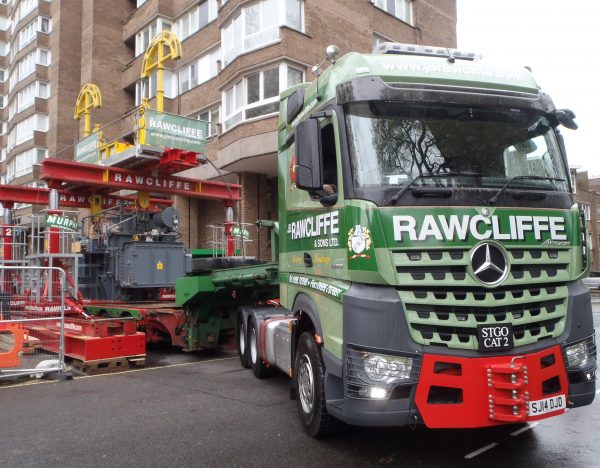
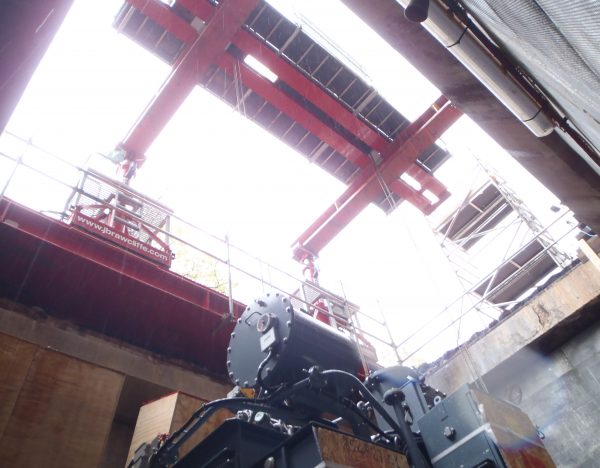
United Lifting In Central London
JB Rawcliffe & Sons Ltd has enhanced its experience in technical handling of heavy equipment with the lifting of transformers in central London utilising strand jack technology. With the transformer located 8m beneath a car park, JB Rawcliffe & Sons Ltd were tasked with providing a solution to remove a transformer from its operation position and replace with it a new transformer.
The solution involved the utilisation of JB Rawcliffe & Sons Ltd hydraulic lift system and stand jack technology were the two components were united to produce a unique jacking system with an unlimited lifting capability.
The redundant transformer was lifted from its operating position 8m below ground level and loaded directly to transport in one simple and safe operation. The replacement transformer was placed to its operating position by the same safe and simple operation but in reverse.
All the engineering, planning and sleepless nights were rewarded with a successful project which was completed safely within schedule.
More details can be found and downloaded in our Case Studies section of the website.